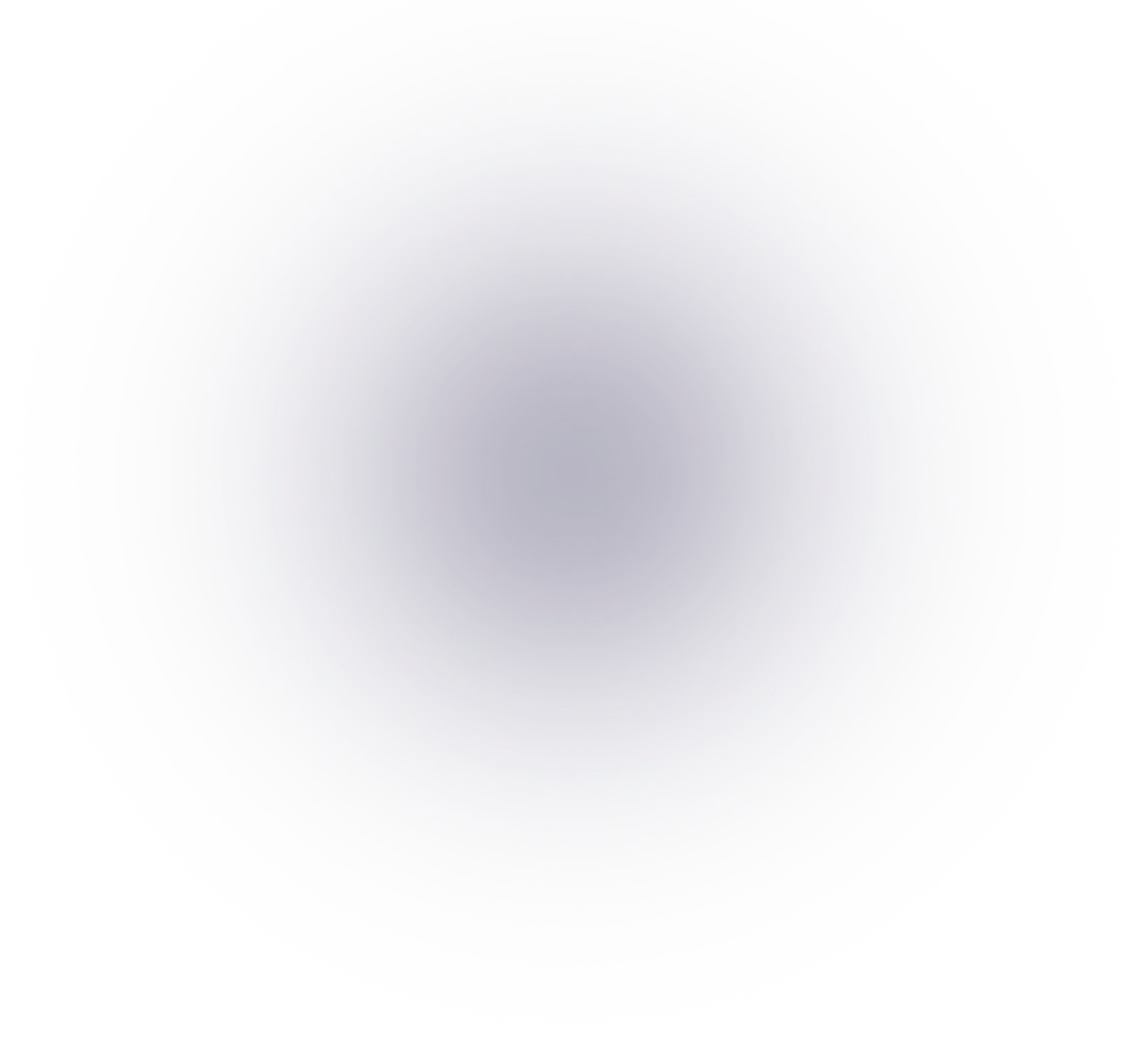
8 Ways TrulinX Simplifies Business for Industrial Pump Distributors
Industrial pumps have to be able to perform in unforgiving environments and in high-use applications, whether moving chemicals, oil and petroleum, water and wastewater, food, or other materials. The same goes for ERP software for industrial pump distributors. It has to perform a variety of functions and make it easy to do so for tighter control on inventory and workflow and increased efficiencies and profitability.
Tribute’s flagship product, TrulinX, and its work order management (WOM) tool, was created to make business easier for distributors in the pump industry. TrulinX goes beyond ERP capabilities, also serving as powerful pump repair tool. Tribute developed a Pump Specification Verification Form that allows an employee to cover all specifications required for a pumping project during a customer call or email. This information is also retained in TrulinX in the event of changes or a manufacturer’s error down the road. Once the template is populated with the pump requirements, it can be converted to a quote that gets sent to the shop or outside fabricator.
Here are eight ways TrulinX software helps you gain greater control of your distribution business.
An Easy, Flexible User Interface
With an easy and flexible Bill of Materials (BOM) interface in the TrulinX Work Order Module (WOM), users can drag and drop components. Subassemblies can be created in TrulinX, while the WOM tool enables the use of permanent structures and on-the-fly structures at any level of the bill. Users can also source, expedite and route all within the same screen. Substituting components or checking availability at other locations for components that are constrained can also be done.
Create Work Orders Independently for Build to Stock
Work orders can be entered directly for Build to Order or created separately for Build to Stock Orders. This feature is extremely useful for activities such as repairs, estimates or when selling standard industrial pumps to certain industries, where it’s important to always stock a few of each standard model.
Work-in-Process Inventory
An assembly can be labeled as a fabrication, which will move components to ‘work-in-process’ inventory while the assembly is being finished. For the movement of components, there are multiple options available. It’s easy to move components from one job to another; components purchased specifically for a job can be routed straight to the job when received. Work in process can be listed and expedited for a particular job whenever desired through reports and inquiries.
Application of Labor & Burden
Enter estimates of both labor and burden. Estimates entered are used to help determine the cost when jobs are partially completed. The actual costs applied are also tracked throughout the process. When the job is done, the costs will be reconciled and a comparison made available at the subassembly and assembly levels of the job. TrulinX will keep track of inventory items used, as well as costs by category. Users can have any number of labor and burden lines and the labor and burden will be accumulated for each subassembly as well as for the entire job.
Routing Options for Pump Assembly
Choose who will complete a BOM or any subassembly within that BOM structure from a variety of options: internal assembly; the entire assembly or one or more subassemblies are built at another location; or, an outside vendor builds the entire assembly or one or more subassemblies. It’s then easy to route an assembly from one source to another. The final destination of the completed assembly can also be controlled with shipping papers generated to help warehouse personnel and outside vendors route products correctly.
Serial Number Tracking for Pump Assemblies or Components
Tracking the serial number of a pump and/or its components is easy. Simply enter the serial number of an assembled pump or its components as it comes in from suppliers. TrulinX will store the information for warranty and preventative maintenance, as well as for tracking them throughout the assembly process. There is also an auto-generating serial numbers feature for pumps built in your shop. A new serial number can be automatically generated along with a label whenever a work order is generated for a built item.
Heat/Batch/Lot Control for Pump Inventory
Track lots, heats and batches based on PO receipt lines to manage pump inventory with the TulinX Lot Control System. Customer service can have access to real-time information by entering key data, such as the date received and the lot. A First In, First Out (FIFO) feature helps make sure the oldest inventory is used first to avoid scrap or aged inventory.
Pump Service/Repair Management
TrulinX also acts as pump repair software with its ability to incorporate key information all on one screen—receiving a customer’s pump, inspecting it and quoting the customer. To be profitable on each job, it’s critical to manage the estimating and actual repair process. TrulinX is powerful pump repair software that has the tools to tightly manage each step along the way to properly capture labor, overhead and part costs.
Disposition Management
Pump distributors who also run repair and rebuild shops often find themselves with a lot of scrap metal at the end of each month or quarter. Some pump distributors buy back old pump cores from their customers in order to refurbish or sell them back to a remanufacturer. This practice helps their customers get rid of old parts, while the distributor can make an additional income by selling new, used, or remanufactured parts - thus avoiding the scrap yard.
TrulinX is designed to help pump distributors manage their scrap and core returns in the following scenarios:
- A distributor is building or repairing a pump and during the process, the customer notifies of a needed change: This can either be marked as Scrap to Order and customer is responsible for the scrap charge, or return to stock if the part has not been altered in any way.
- A distributor is building or repairing a pump and a part is mishandled or damaged during production: The distributor is responsible for the damaged part and scrapped to COGS.
- A customer determines a change is needed to a part before production begins: TrulinX will allow you to transfer the part back into stock and do a simple inventory adjustment.
- If a distributor deals with cores, TrulinX will allow a core charge to be added to the sale of the product and then when returned, will be given a credit.
Upgrade Your Business to TrulinX ERP Software Today
Ready to gain better control of your pump distribution business? Request a demo of TrulinX to learn more about how our ERP software can help you create efficiencies, maximize profits and better serve your industrial pump customers.